¿Cómo se fabrica la RAM?
¿Alguna vez se ha preguntado de qué está hecha la RAM y cómo se fabrica la memoria? A continuación ofrecemos un vistazo entre bastidores del riguroso proceso que llevamos a cabo para fabricar memorias y garantizar que obtiene un producto de alta calidad.
Existen varios tipos de memoria, pero todos se fabrican de la misma manera. Continúe leyendo aquí para obtener más información sobre las propiedades de los diferentes tipos de memoria. Continúe leyendo aquí para obtener más información sobre los diferentes tipos de memoria de servidor.
Parte I: Del silicio a la retícula terminada
Los chips de memoria son circuitos integrados con varios transistores, resistencias y condensadores que deben formarse en cada uno de los chips. Estos circuitos integrados comienzan como silicio, que generalmente se extrae de la arena. Convertir el silicio en chips de memoria es un procedimiento riguroso y meticuloso en el que participan ingenieros, metalúrgicos, químicos y físicos. La memoria se produce en una gran instalación llamada fab, que contiene muchos entornos de sala limpia. Los chips de memoria semiconductores se fabrican en salas limpias porque los circuitos son tan pequeños que incluso pequeñas partículas de polvo pueden dañarlos. Las instalaciones principales de Micron en Boise, Idaho, cubren más de 167 225 metros cuadrados y tienen salas limpias de clase 1 y clase 10. En una sala limpia de clase 1, no hay más de 1 partícula de polvo en un pie cúbico de aire. En comparación, un hospital limpio y moderno tiene aproximadamente 10 000 partículas de polvo por pie cúbico de aire. El aire dentro de una sala limpia se filtra y circula continuamente. Los miembros del equipo de producción usan gorros, batas y máscaras especiales que ayudan a mantener el aire libre de partículas.
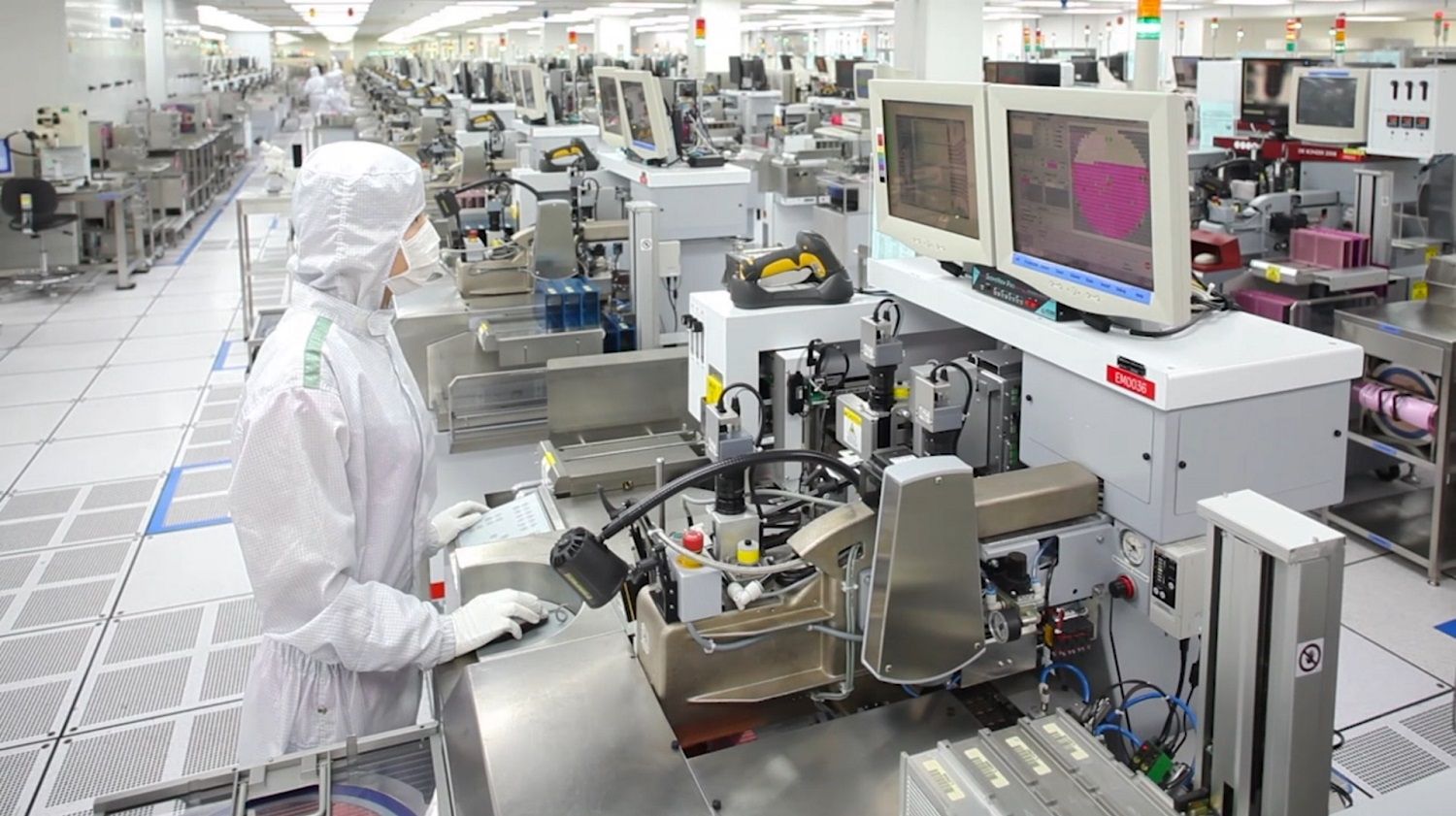
Paso 1: Lingotes de silicio
El primer paso del silicio al circuito integrado es la creación de un cilindro o lingote puro de un solo cristal, que está hecho de silicio y que tiene 330 milímetros de diámetro. Una vez formados, los lingotes de silicio se cortan en obleas muy finas y pulidas con menos de 6 milímetros de grosor. Los elementos del circuito del chip (transistores, resistencias y condensadores) se construyen luego en capas en la oblea de silicio. Los circuitos se desarrollan, se prueban mediante simulación y se perfeccionan en los sistemas informáticos antes de que realmente se construyan. Cuando se completa el diseño, se hacen fotomáscaras de vidrio: una máscara para cada capa del circuito. Las fotomáscaras son placas opacas con orificios o transparencias que permiten que la luz brille en un patrón definido. Estas máscaras son esenciales para el siguiente paso en el proceso de fabricación: la fotolitografía.
Paso 2: Fotolitografía
En el ambiente estéril de la sala limpia, las obleas están expuestas a un proceso de fotolitografía de múltiples pasos que se repite una vez para cada máscara requerida por el circuito. Se utilizan máscaras (a) para definir las diferentes partes de un transistor, condensador, resistencia o conector que completará el circuito integrado y (b) para definir el patrón de circuito para cada capa en la que se fabrica el dispositivo. Al comienzo del proceso de producción, las obleas de silicio desnudas se cubren con una capa delgada de vidrio, seguida de una capa de nitruro. La capa de vidrio se forma al exponer la oblea de silicio al oxígeno a temperaturas de 900 grados Celsius durante una hora o más, dependiendo de qué tan gruesa debe ser la capa. El vidrio (dióxido de silicio) se forma cuando el material de silicio en la oblea se expone al oxígeno. A altas temperaturas, esta reacción química (llamada oxidación) ocurre a un ritmo muy rápido.
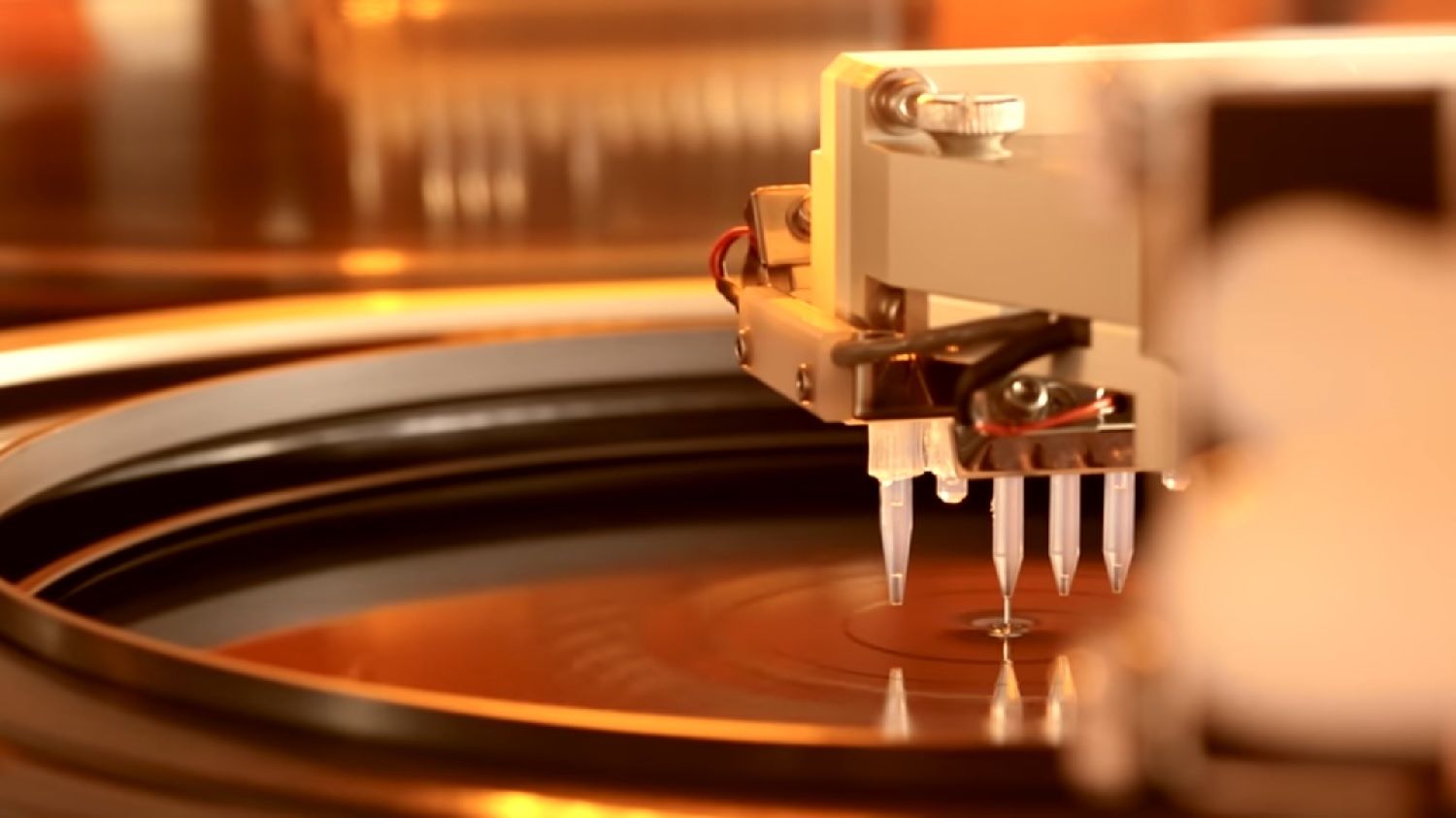
Paso 3: Fotorresistente
A continuación, la oblea se recubre uniformemente con un líquido espeso sensible a la luz llamado fotorresistente. Las porciones de la oblea se seleccionan para exposición alineando cuidadosamente una máscara entre una fuente de luz ultravioleta y la oblea. En las áreas transparentes de la máscara, la luz atraviesa y expone el fotorresistente. Cuando se expone a la luz ultravioleta, la fotoprotección sufre un cambio químico, que permite que una solución reveladora elimine la fotorresistencia expuesta y deje una porción no expuesta en la oblea. Para cada máscara requerida por el circuito, se repite el proceso de fotolitografía/fotorresistencia.
Paso 4: Grabado
En la etapa de grabado, se coloca gas seco de plasma o ácido húmedo sobre la oblea para eliminar la parte de la capa de nitruro que no está protegida por la fotoprotección endurecida. Esto deja un patrón de nitruro en la oblea en el diseño exacto de la máscara. Cuando la fotorresistencia endurecida se elimina (limpia) con otra sustancia química, cientos de chips de memoria ahora pueden grabarse en la oblea.
Parte II: Realizar capas a la oblea y completar el circuito
En la Parte I del proceso de fabricación, todos los elementos del circuito (transistores, resistencias y condensadores) se construyeron durante las operaciones iniciales de la máscara. Los siguientes pasos conectan estos elementos creando un conjunto de capas.
Paso 5: Capas de aluminio
Para comenzar a conectar los elementos del circuito, se deposita una capa aislante de vidrio (llamada BPSG) sobre la oblea, y se usa una máscara de contacto para definir los puntos de contacto (o ventanas) de cada uno de los elementos del circuito. Después de que las ventanas de contacto se graben, toda la oblea se cubre con una fina capa de aluminio en una cámara de pulverización. Cuando se aplica una máscara de metal a la capa de aluminio, se forma una red de conexiones metálicas finas o alambres, creando un camino para el circuito.
Paso 6: Capas de pasivación
La oblea completa se cubre con una capa aislante de vidrio y nitruro de silicio para protegerla de la contaminación durante el ensamblaje. Esta capa protectora se llama capa de pasivación. A continuación, se realiza una máscara final y un proceso de grabado de pasivación, eliminando el material de pasivación de los terminales, que se llaman denominan áreas de conexión. Las áreas de conexión ahora libres se utilizan para conectar eléctricamente el dado a las clavijas de metal en el paquete de plástico o cerámica, y el circuito integrado ya está completo. Antes de enviar la oblea al ensamblaje de dado, se prueban todos los circuitos integrados de la oblea. Los chips funcionales y no funcionales se identifican y mapean en un archivo de datos del ordenador. Una sierra de diamante luego corta la oblea en chips individuales. Los chips no funcionales se descartan y el resto está listo para ensamblarse. Estos chips individuales se conocen como dados. Antes de que se encapsulen los dados, se montan en bastidores de conductores donde los delgados alambres dorados conectan las áreas de conexión del chip con los bastidores para crear un camino eléctrico entre el dado y los alambres de plomo.

Parte III: Preparación y prueba de dados
En la Parte II del proceso de fabricación, se creó el circuito integrado y la oblea terminada se cortó en dados. En los próximos pasos, se preparará el dado para su uso en módulos terminados.
Paso 7: Encapsulación
Durante la encapsulación, los bastidores de conductores se colocan en placas de molde y se calientan. El material plástico fundido se aprieta alrededor de cada dado para formar su paquete individual. El molde se abre y los bastidores de conductores se presionan y se limpian.
Paso 8: Galvanoplastia
La galvanoplastia es el siguiente proceso donde los bastidores de conductores encapsulados se "cargan" mientras se sumergen en una solución de estaño y plomo. Aquí, los iones de estaño y plomo son atraídos al bastidor de conductores cargado eléctricamente, lo que crea un depósito uniforme enchapado, que aumenta la conductividad del dado y proporciona una superficie limpia para poder montar el dado.
Paso 9: Recorte y forma
En el recorte y la forma, los bastidores de conductores se cargan en máquinas de recorte y forma, donde se forman conductores y luego se cortan los chips de los bastidores. Los chips individuales se colocan en tubos antiestáticos para su manipulación y transporte al área de prueba para la prueba final.
Paso 10: Prueba de resistencia a quemado
En las pruebas de resistencia a quemado, cada chip se prueba para ver cómo funciona en condiciones de esfuerzo acelerado. Esta prueba de resistencia es un componente fundamental para la fiabilidad del módulo. Al probar los módulos en condiciones de esfuerzo acelerado, podemos eliminar los pocos módulos en cada lote que fallarán después de un uso mínimo. Para llevar a cabo pruebas de resistencia a quemado, utilizamos los hornos AMBYX líderes de la industria que nuestros ingenieros desarrollaron específicamente para las pruebas de resistencia. Una vez que los chips de memoria pasan la prueba de resistencia, se inspeccionan, sellan y preparan para su ensamblaje.
Paso 11: Ensamblaje y construcción de PCB
Una vez que se hacen los chips de memoria, necesitan una forma de conectarse a la placa base de su ordenador. Las tarjetas de circuito impreso (PCB) resuelven este problema ya que proporcionan una forma de conectar los chips a la placa base. Para lograr esto, los chips se montan en una tarjeta de circuito impreso (PCB) y el producto final es un módulo de memoria terminado. Las PCB están construidas en matrices o láminas, que se componen de varias tablas idénticas. Después del ensamblaje, la matriz se separa en módulos individuales, de forma similar a cómo se puede dividir una barra de chocolate en cuadrados más pequeños. Al variar la cantidad total de PCB en cada matriz según el tamaño, Micron maximiza la cantidad de módulos fabricados a partir de una cantidad dada de materias primas.
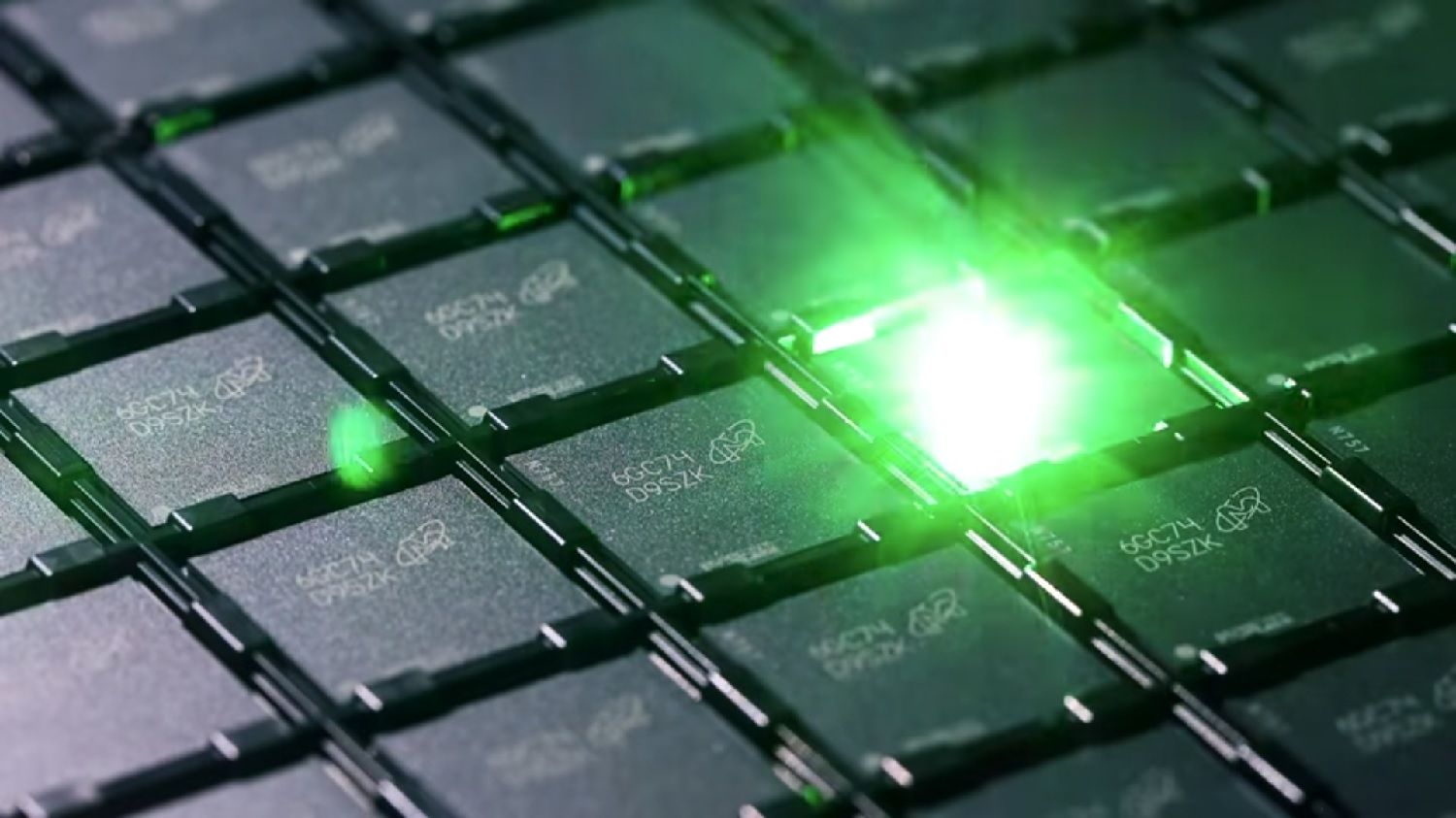
Parte IV: Ensamblaje del módulo
En la Parte III del proceso de fabricación, el dado y la PCB se prepararon para el ensamblaje final del módulo. Los pasos finales cubren el proceso de ensamblaje del módulo.
Paso 12: Impresión de pantalla
Cuando se perfecciona el diseño del módulo y se producen las PCB, comienza el montaje del módulo de memoria. El montaje implica un intrincado procedimiento de soldadura que conecta chips de memoria a la PCB. Esto comienza con la impresión de pantalla. En la impresión de pantalla, se utiliza una plantilla para filtrar pasta de soldadura sobre la PCB terminada. La pasta de soldadura es una sustancia pegajosa que mantiene los chips en su lugar en la PCB. El uso de la galería de símbolos garantiza que la pasta de soldadura se adhiera solo donde se unirán los componentes (chips). Los puntos de unión son fáciles de localizar gracias a los marcadores fiduciarios, que son marcas en la PCB que determinan el lugar en donde se deben colocar los chips. Una vez aplicada la pasta de soldadura, unas máquinas automatizadas de “recogida y colocación” escanean los marcadores fiduciarios para determinar en dónde colocar los chips en la PCB. Los dispositivos de recogida y colocación están programados para saber qué chips se colocan en el lugar, de modo que cuando una máquina toma un chip de un alimentador y lo coloca en la PCB, sabe exactamente dónde está el chip. El proceso de colocación de chips ocurre para todos los chips restantes y para cualquier otro componente en el módulo. De todos los pasos en la fabricación de memoria, este es el más rápido: ¡los chips se colocan en una PCB acabada en solo unos segundos!
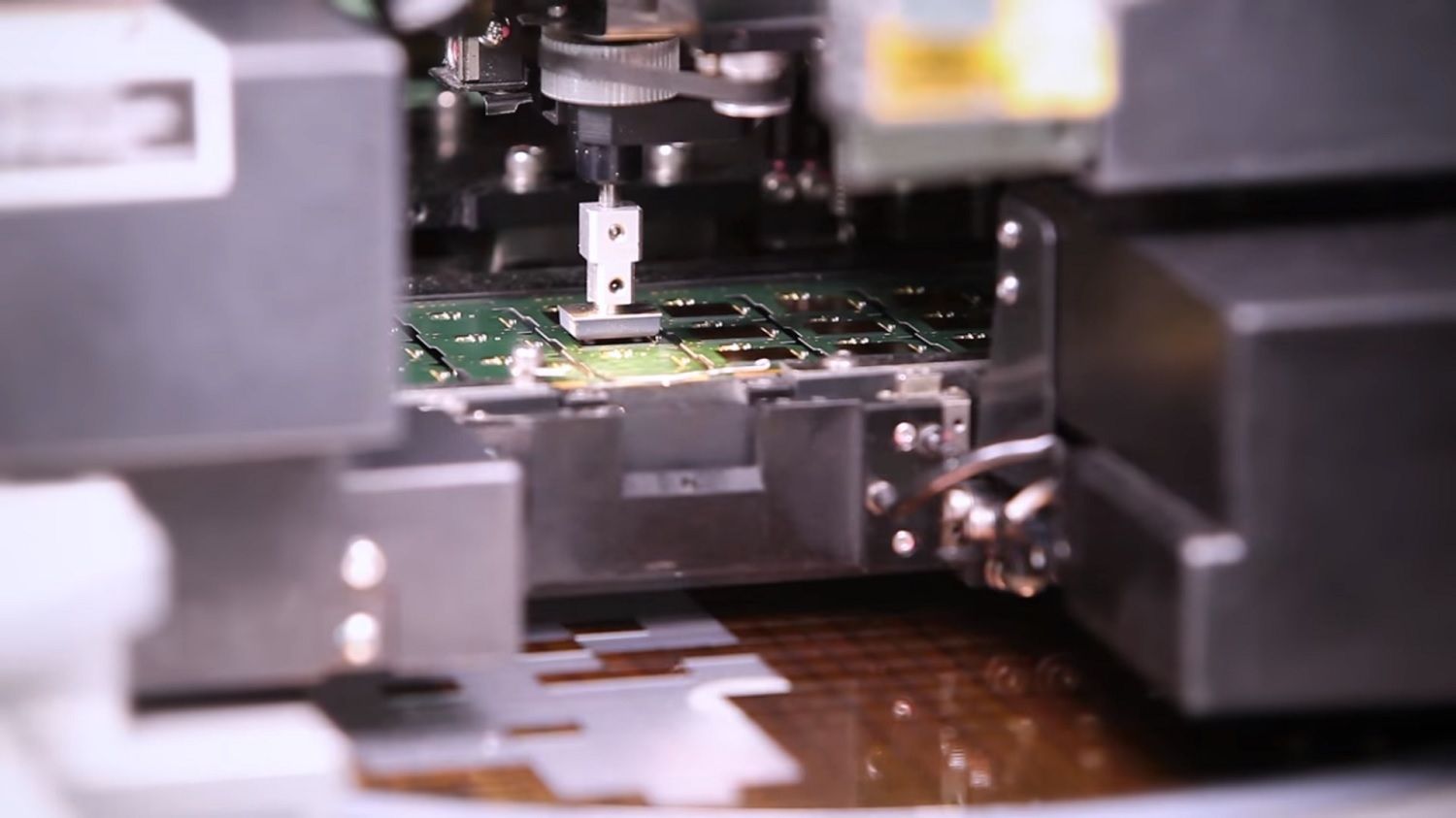
Paso 13: Soldadura y fijación
A continuación, los chips y tableros ensamblados pasan a través de un horno. El calor derrite la pasta de soldadura en un líquido. Cuando la soldadura se enfría, se solidifica, dejando una unión permanente entre los chips de memoria y la PCB. La tensión superficial de la soldadura fundida evita que los chips se desalineen durante este proceso. Una vez que los chips están unidos, la matriz se separa en módulos individuales. Los miembros del equipo de Micron inspeccionan visualmente cada módulo. Muchos módulos también se someten a inspecciones adicionales utilizando equipos automáticos de rayos X para garantizar que todas las juntas se hayan soldado adecuadamente. Todos los módulos de memoria Micron cumplen con los criterios de aceptación IPC-A-610, el estándar de la industria reconocido en todo el mundo.
Paso 14: Pruebas de calidad posteriores al ensamblaje
Micron luego prueba y etiqueta los módulos. Usamos equipos personalizados para probar automáticamente el rendimiento y la funcionalidad. Esto elimina la posibilidad de que un operador coloque erróneamente un módulo defectuoso en una ubicación de paso. Ciertos módulos están programados con una "etiqueta de identificación" que su ordenador reconocerá y leerá.
Paso 15: Envío
Antes de enviarse a fabricantes y consumidores de ordenadores, una porción estadísticamente significativa de los módulos terminados se selecciona aleatoriamente para una inspección de calidad final. Una vez aprobados los módulos para su uso, se colocan en bandejas y bolsas de plástico aptas para ESD y se preparan para la entrega. Después de un extenso proceso de fabricación, su memoria está lista para usar. ¡Ha sido rigurosamente probada y aprobada! Continúe leyendo aquí para obtener más información sobre las unidades de memoria.
©2018 Micron Technology, Inc. Todos los derechos reservados. La información, los productos y las especificaciones están sujetos a cambios sin previo aviso. Ni Crucial ni Micron Technology, Inc. se responsabilizarán por las omisiones u errores que pueda haber en la tipografía o en las fotografías. Micron, el logotipo de Micron, Crucial y el logotipo de Crucial son marcas comerciales o marcas comerciales registradas de Micron Technology, Inc. Todas las demás marcas comerciales y marcas de servicio son propiedad de sus respectivos propietarios.